Introducing 3:1 heat shrink tubing to have you labeling like a Pro
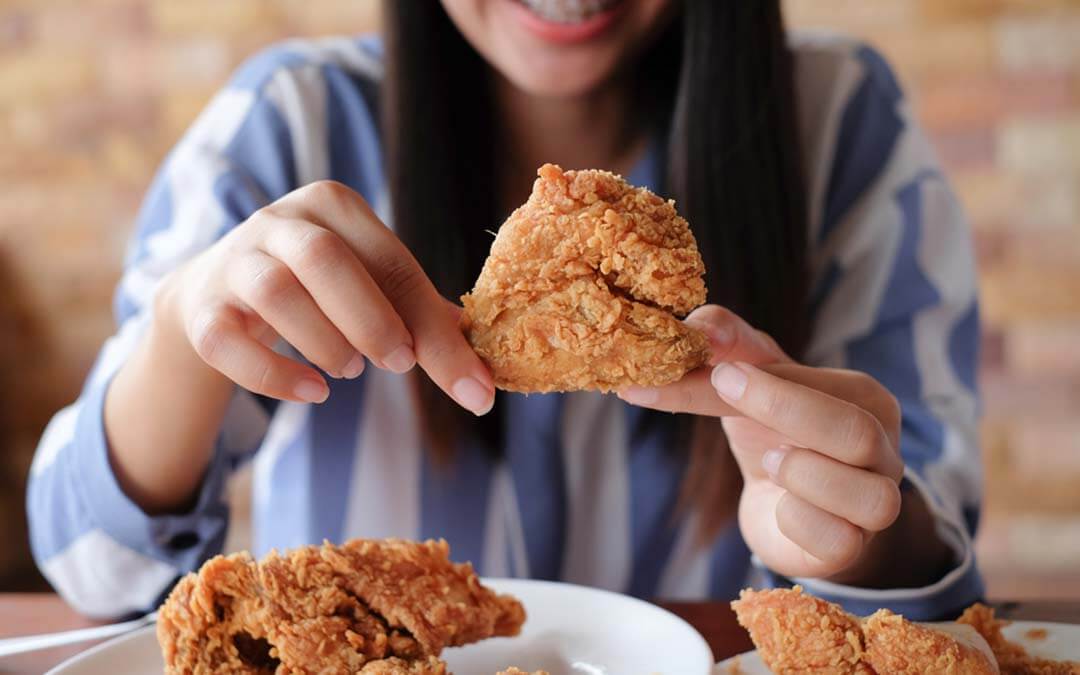
National Food Service Provider Finds the Recipe to Inventory Control Success
With on-demand QuickDeploy Mobile Labeling Kits from Brother
For today’s food service companies, capturing the correct SKUs and prices at the point of sale (POS) can be extremely difficult when the same food items can be sold as part of a combo meal or a la carte.
Tracking and managing inventory becomes even more complex when food items are packaged in bags that prevent easy identification of the contents. If product is captured inaccurately at the POS, it can be daunting to reconcile inventory and “cash-in-till.”
This was precisely the problem faced by a large fried chicken food service company – a business serving more than 2,000 gas stations and convenience stores throughout the U.S. with a turnkey fried chicken preparation and production business unit.
The company’s customers were placing orders at the preparation and production area and choosing from as many as 50 main course and side dishes. Their orders were then placed in bags for them to take to the cashier. At checkout, customers were instructed to detail their food order to the cashier verbally and pay. This time-consuming approach created unnecessarily long lines at the cashier station and often led to incorrect POS entries – a primary cause of shrinkage in the food service industry.
Cooking up a solution
The company’s leaders and staff realized that barcoding the food bags with the items purchased upfront would allow for quick, efficient scanning at checkout. The challenge was finding a single, simple way to create barcode labels for every single store without requiring a new software development effort for each of the location’s unique POS systems.
The Brother TD-2100 QuickDeploy Mobile Labeling Kit, a stand-alone inventory control labeling solution, proved to be the answer. This combination printer/scanner kit contains virtually everything needed to properly label items as they’re packaged in the food prep area, including a state-of-the-art desktop thermal printer and the following custom features:
- The company’s 100-item menu file resident in the printer
- A barcode scanner connected to the printer’s USB port
- Laminated menu “scan cards” to activate label printing
Even better, the easy-to-operate solution arrives at the stores preconfigured and ready to use right out of the box. Setting up the solution takes only a few minutes – with no extensive operator training required. All the operators need to do is connect the printer to AC power, load the label roll into the printer, and connect the scanner (included in the box) to the USB port on the printer.
Making fast food faster
Today, customers of the food service company place orders at the preparation and production area as before. However, as items are placed in the bag, the laminated menu cards are scanned to produce the corresponding barcode labels for each item. These labels are placed on the outside of the bag so that cashiers can quickly and easily scan the correct items at checkout – helping ensure the right food items are accurately recorded in the POS.
Eating up the benefits
Thanks to the TD-2100 QuickDeploy Mobile Labeling Kit from Brother, the national food service company went from fretting over inventory control to discovering an irresistible recipe for success. The benefits of this solution have included:
- A truly stand-alone solution, without the need for a laptop or POS connection
- Accurate item sales counts for inventory reconciliation
- Proper price capture at the POS with barcode scanner
- Reduced shrinkage with more accurate production forecast data
- Decreased customer wait times with more efficient sales processing at the sales counter
Brother QuickDeploy Mobile Labeling Kits
For the easy approach to on-demand labeling, think inside the box.
With these versatile, stand-alone solutions, retail and convenience stores, food service operations, and warehouses get virtually everything they need to print labels, tags, and barcode labels in as little as 24 hours – all a fraction of the cost of traditional mobile printing options. Perfect for budget-conscious retailers and rapid prototyping projects, QuickDeploy Mobile Labeling Kits require no integration, no Wi-Fi® connectivity, and no recurring fees.